Ammonia Cracker Unit
High-quality Ammonia Cracker Units for efficient hydrogen production from ammonia.
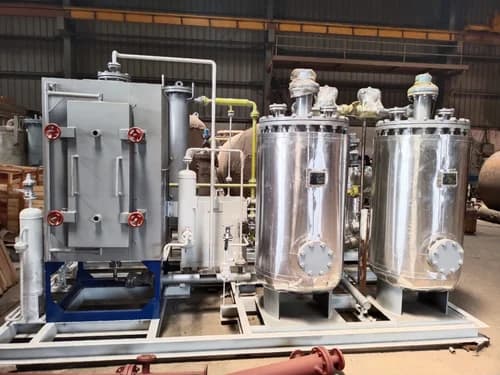
Product Overview
Ammonia Cracker Units are designed to produce hydrogen by cracking ammonia at high temperatures. The process involves the thermal decomposition of ammonia into hydrogen and nitrogen.
Our Ammonia Cracker Units are engineered to provide a reliable and efficient source of hydrogen for various industrial applications. The units are fully automatic and require minimal operator intervention.
Applications
- Heat treatment processes
- Metallurgical industries
- Chemical processing
- Electronics manufacturing
- Glass industry
- Fuel cell applications
Technical Specifications
Process Description
The ammonia cracking process involves the following steps:
- Ammonia is fed from cylinders or a storage tank to the cracking furnace.
- In the cracking furnace, ammonia is heated to temperatures between 800-900°C.
- At these temperatures, ammonia (NH₃) decomposes into nitrogen (N₂) and hydrogen (H₂).
- The resulting gas mixture contains approximately 75% hydrogen and 25% nitrogen.
- Optional purification systems can be added to obtain higher purity hydrogen if required.
Standard Features
- Fully automatic operation
- PLC based control system
- High-efficiency cracking furnace
- Safety interlocks and alarms
- Optional hydrogen purification system
- Capacities from 10 to 1000 Nm³/hr
Advantages of Ammonia Cracker
Our Ammonia Cracker Units offer numerous benefits for hydrogen production.
Cost Effective
Economical hydrogen production compared to electrolysis or steam methane reforming.
Reliable Operation
Simple process with minimal moving parts ensures high reliability and uptime.
Easy Storage
Ammonia is easier to store and transport than hydrogen, making it an efficient hydrogen carrier.
On-Demand Production
Generate hydrogen as needed, eliminating the need for large hydrogen storage systems.
Scalable Solution
Units available in various capacities to match your specific hydrogen requirements.
Low Maintenance
Minimal maintenance requirements result in lower operating costs and reduced downtime.
PSA Hydrogen Purification Units
High-purity hydrogen generation systems using Pressure Swing Adsorption technology.
Product Overview
PSA Hydrogen Plants use Pressure Swing Adsorption technology to purify hydrogen from various feed gases. The process involves selective adsorption of impurities on molecular sieves, allowing pure hydrogen to pass through.
Our PSA Hydrogen Plants can achieve hydrogen purities up to 99.9%, making them suitable for a wide range of applications requiring high-purity hydrogen. The systems are fully automatic and designed for continuous operation.
Applications
- Hydrogenation processes
- Fuel cell applications
- Metallurgical processes
- Electronics manufacturing
- Chemical processing
- Pharmaceutical industry
Technical Specifications
Process Description
The PSA hydrogen purification process involves the following steps:
- Feed gas (reformate) containing hydrogen and impurities enters the PSA system.
- The gas passes through adsorber vessels containing molecular sieve adsorbents.
- Impurities such as CO, CO₂, CH₄, N₂, and water vapor are selectively adsorbed.
- Pure hydrogen passes through and is collected as product gas.
- The adsorber vessels are regenerated by depressurization and purging, creating a continuous cycle.
Standard Features
- Hydrogen purity: up to 99.9%
- Capacity: 10-500 Nm³/hr
- Fully automatic operation
- PLC based control system
- High hydrogen recovery rate
- Low maintenance requirements
Advantages of PSA Hydrogen Plants
High Purity
Achieve hydrogen purities up to 99.9999%, suitable for the most demanding applications.
Energy Efficient
Low energy consumption compared to alternative purification methods like cryogenic separation.
Modular Design
Scalable systems that can be expanded to meet increasing hydrogen demand.
Continuous Operation
Multiple adsorber vessels operating in sequence ensure uninterrupted hydrogen supply.
Automatic Control
PLC-based control system with minimal operator intervention required.
Quick Startup
Rapid startup and shutdown capabilities for flexible operation.
Ready to Get Started?
Contact our team to discuss your hydrogen requirements and get a customized solution.